Design & Operation of Wind Farm Support Vessels

01.06.2015
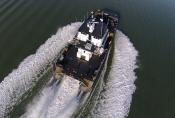
Design & Operation of WFSV - by John Haynes
Offshore wind farm development has been led globally by the UK, followed by Germany.
Both the UK and Germany have governments with long term commitments to renewable energy.
Denmark, Belgium and The Netherlands are building wind farms, but they are a long way behind the leaders in offshore wind.
In 2014 the UK accounted for over 50% of all the offshore wind energy generated globally. All of these countries border the North Sea, a notoriously stormy sea area, which has a high frequency of wind to drive the turbines.
Traditional survey vessels are first to arrive in a potential wind farm area. Typically the seabed owner wants to ensure that there are no hazards or obstructions before offering leases. Once leases are granted commercial developers will then carry out their own surveys to confirm depths and seabed data plus investigate typical wind and sea conditions before construction begins. Compared to oil and gas sector drilling surveys this is straightforward work for offshore survey vessels and their crews.
Wind Farm Construction Phase
First stage of wind farm installation typically involves heavy lift construction vessels and construction support vessels. Tasks for installation vessels include the transfer of support structures and turbines offshore. On site these vessels establish bases for lifting and installation operations.
These vessels can also provide offshore access and accommodation for crew. This phase of the installation process includes transportation of the nacelle, hub assembly, blades, towers and array cables from construction port to site.
Once the wind farm construction phase is underway the first sub IMO / sub 80 feet vessels on site are Wind Farm Service Vessels (WFSV) which can overlap roles with Crew Transfer Vessels (CTV). The multi role WFSV enables fast personnel transfer with the capability for utility work such as moving equipment, delivery of spares, enforcing safety zones, conducting environmental studies and providing support for divers.
Specifically Developed Vessels for Supporting Wind Farms
Current fleets of Wind Farm Service Vessels have been specifically designed to work in the wind farm support sector. As with the North Sea oil and gas industry, in the early days of wind farms, former fishing boats were used for a wide range of tasks.
As catamarans offer reduced resistance to motion and reasonable stability they are now the hull form of choice for most WFSV working in northern European waters.
As the demand for wind farm support has intensified, vessels have been specifically developed for transiting to wind farms in a wide range of conditions then delivering technicians onto wind farm turbines.
The cover image, shot from a remote controlled gyrocopter, is of ‘Seacat Intrepid’ owned by UK operator Seacat Services. Launched in 2014, she is a 26 metre (85 feet) South Catamaran from UK builder South Boats IOW with design by Alicat Marine Design. Propulsion for this new Wind Farm Service Vessel is via 2 x Rolls Royce 56A3 waterjets powered by a pair of MTU 1450HP diesel engines.
These specialist designs comprise of a pair of hulls reinforced by substantial vessel superstructure and high bridge position, which gives good line of sight for the captain when embarking personnel or cargo from the bow. Vessels have evolved with improved underwater hull shapes to reduce engine power requirements and reduce fuel costs, which are a significant part of operation and maintenance costs.
When boats are chartered to a wind farm the boat owner provides vessel and crew for a fixed period with fuel costs usually borne by the wind farm operator.
In the early stages of wind farm development vessel ranged from 15 to 18 metres (50 to 60 feet). Due to the International Load Line convention vessels are typically delivered below 24 metres LLL (Load Line Length). In recent years the majority of vessels have been designed to 24 metres with wide beams to get maximum working space and payload onboard. A large ratio of length to width enables vessels to travel at planing speeds with good lateral stability and reduced vertical motion.
Vessel coding or classification ensures that vessels are built and equipped to a recognized standard. The majority of European WFSVs are coded by national authorities to operate up to 60 miles from a safe haven. As wind farms go further offshore vessels will need to be more capable and it is normal practice to be certificated by a recognised classification society such as DNV–GL.
WFSV catamarans, generally constructed in aluminium or GRP composite, can currently accommodate up to 12 passengers. The operations which transport technicians to wind farms for maintenance typically drop off teams of three technicians at each turbine for the day’s work. Recent conferences, including the January 2015 Royal Institution of Naval Architects conference ‘Design & Operation of Wind Farm Support Vessels’ have demonstrated that industry now wants to move more personnel on a single vessel. There are ongoing discussions between the IMO, national legislators and classification societies to create a revised interpretation of ‘industrial personnel’ to raise the numbers of professional passengers on vessels servicing the offshore energy industry. Commercial pressures are relevant, but safety and compliance are driving the debate.
A 24 metre catamaran may be required to carry up to 30 tonnes of cargo. When moving technicians transit speeds range between 20 and 25 knots with some vessels having a top speed of 30 knots. Fixed pitched propellers are used to drive around 50% of WFSV. Water jets are used on around 40% of the current fleet. Water jets offer good manoeuvrability and the shallow draft can be essential on some offshore wind farm sites. Other propulsion systems include controlled pitched propellers (CPP) with various new systems under trial and evaluation.
Once the wind farm is completed and connected to the grid preventative maintenance and corrective maintenance are ongoing tasks for WFSVs. The schedule of visits to turbines includes routine surveys and inspections. The aim is to keep the entire wind farm ready to generate wind for the maximum number of days per year. Preventative maintenance programmes are designed to decrease the number of failures, limit downtime and extend the life time of the turbine, foundation and associated components.
Transit time and accessibility to the wind farm are often weather dependent. In the North Sea sites further from shore typically experience larger significant wave heights. Transferring maintenance personnel and their equipment from vessel to wind turbine safely in various sea states is a major challenge in offshore wind farm operations. The turbine foundation is fixed to the seabed resulting in considerable relative movement between the vessel and the structure. Turbine transfers, known in the industry as ‘bump and jump’, are where a vessel uses engine power to push the bow against ‘j-tubes’ which run vertically on the outside of the turbine access ladder. Thrust is applied to increase friction and reduce motion between specially designed bow fenders and the landing platform. Maintenance technicians step onto the turbine access ladder which is set back from the j-tubes providing a safety zone to prevent personnel on the ladder from being crushed. Large waves, especially when coupled with strong currents, can cause the vessel to lose position or contact with the turbine. Current technology and vessel designs limit this operation to 1.5 metre (5 feet) significant wave heights.
Turbine transfers can be assisted by passive or active motion compensating systems. Vessels fitted with damping systems aim to reduce vessel motion enabling transfer operations in rougher sea conditions. These systems monitor vessel accelerations caused by wave motion and constantly compensate to reduce the relative motion between the vessel and turbine structure. Systems include the MaXccess, Momac, Amplemann and Houlder TAS systems. On the down side their inclusion in vessel design increases purchase costs, raises weight on deck and reduces working deck space. A long term industry aim is to improve the economic viability of wind farms by widening the crew transfer weather window to include significant wave heights above 1.5 metre.
With boat crews and technicians spending their working lives at sea, often on station for 7 days at a time with 12 hour shift patterns, passenger and crew comfort onboard has become a priority. Technicians need to arrive at the wind farm feeling well and rested before transferring to the turbines. Once on the turbine it is a physical working environment and the industry has introduced climbing fitness standards. Vessels use specialist suspension seats which are designed to minimise fatigue and the effects of impacts caused by the motion of the vessel. UK seating and component manufacturer KPM Marine has launched a lightweight modular interior system that enables below deck spaces to be constructed quickly on workboats and professional fast craft. KPM Technical Director Julian Morgan said, ‘Safety, comfort and functionality are essential on the modern vessel. We have designed a range of seats specifically for fast workboats. Our modular units include workstations, storage, heads, showers, galley and bunks. The system is designed to reduce weight plus flooring, ceiling or wall panels can be easily removed for access during the build process or if the vessels role changes in the future.’
Launched in 2014 the South Catamaran 26 metre (85 feet) is the first of a new hull form from UK builder South Boats IOW with design by Alicat Marine Design (AMD). Andy Page, Design and Project Manager at AMD, said, ‘A wealth of hull form development and tank testing, has resulted in this next generation craft. The vessel has been optimised for high speed passage, turbine access and loitering in harsher conditions meaning it has the capability to be utilised in sea areas such as the German North Sea and UK Round 3 wind farm developments that are further offshore.’ Featuring finer initial entry and significantly higher wet deck clearance, the 26 metre is expected to remain operational at 2.5 metre (8 feet) significant wave heights. It is available in twin waterjet, IPS or quad engine CPP configurations. Andy Page added, ‘Alicat and Global Marine Design are now offering the new Alicat 27 metre (88 feet) in 12 man or 24 man configurations with a modular superstructure that facilitates easy conversion for survey roles. Of note is the very high cargo payloads offered by this vessel, potentially up to 60 tonnes.’
2015 sees the first US windfarm support vessels in construction. A 21m WFSV designed by Alicat Marine Design under license from South Boats IOW in the UK is a proven design which is being tailored to suit the US market and US Coast Guard requirements. The vessel is being built by Blount Boats of Rhode Island and will be in operation by 2016.
CTruk is a UK based designer and builder of composite high speed craft. CTruk CEO & Chief Designer Andy White's said, ‘Innovation and R&D are the starting points for every CTruk project and the core of the company’s business. Our objective is to deliver vessels and systems that are fully compliant with the customer’s operational requirements.’ Based on a proven workboat design concept, the CTruk MPC22 is a 22 metre (72 feet) composite twin-hull with 7.6 metre (25 feet) beam and 1.25 metre (4 feet) draft. This fast workboat has a 20 tonne flexible payload capability. CTruk’s patented moveable wheelhouse and flexible deck pod system mean that the vessel can fulfil multiple roles. The vessel can be used to transfer 12 technicians or remove its passenger pod to make use of 72m² (775 ft²) of deck space for cargo and equipment transfer. The vessel utilises the Volvo IPS system for optimal bollard pull and service speeds, further increasing the fuel efficiency of CTruk’s lighter weight composite catamarans. Andy White added, ‘The MPC22 was conceived with offshore wind farms in mind and is designed to safely deal with rougher seas and longer transits.’
German boat builder Abeking and Rasmussen has optimised the Small Waterplane Area Twin Hull (SWATH) design for patrol boats and fast workboats. By reducing the volume of the hull at sea surface and achieving a large proportion of the vessel’s buoyancy beneath the waves a SWATH vessel can be more stable in rough seas at high speeds. SWATH vessels normally have a twin-hull arrangement. The 24m Cat-SWATH 24 Pax from Danish Yachts is the first of a series of carbon composite crew transfer vessels designed and built for the offshore wind industry. With bow and stern thrusters supporting the propulsion of variable pitch propellers the 24m Cat-SWATH can reach speeds of up to 23 knots.
The coastal countries of northern Europe are all experienced maritime nations with access to innovative design, high technology and solid construction expertise that has helped to develop the vessels that support offshore wind. The last ten years has seen the wind farm service vessel market expand significantly with a steady evolution in design as operators aim to become more competitive and meet changing requirements. Key drivers for new designs are fuel efficiency and the ability to access wind farms in higher sea states.
The UK Seawork event in June 2015 includes a panel discussion entitled ‘Windfarm Access Vessels - are catamarans the right solution?’ The panel includes advocates for monohulls plus oil & gas industry type OSVs. As the world starts to look at the viability of ocean energy the current crop of specialist vessels will be considered as the benchmarks that next generation renewable energy support craft will evolve from.
The US Bureau of Ocean Energy Management (BOEM) has seen strong interest in offshore renewable energy projects on the Outer Continental Shelf. BOEM is working closely with various east and west coastal states regarding offshore energy development and is in the process of coordinating federal-state task forces. There are lessons to be learned from northern Europe which accounts for the US ‘start smart’ approach to offshore renewable energy.
All images are copyright NEXT GEN Marine Ltd 2025 unless otherwise stated.
This does not exclude the owner's assertion of copyright over the material.