Viable Hybrid Power Systems for Workboats

22.05.2015
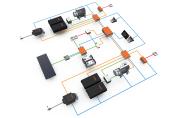
Hybrid Power & Propulsion Systems for Workboats
In 2015 two significant developments are going to make many operators, owners and builders of professional vessels consider hybrid marine power and propulsion systems.
Firstly the new emissions laws in ports and secondly there is now an incentive for high technology manufacturers to invest in developing highly efficient batteries.
Dramatically reducing pollution in both water and air, particularly in ports and around people, could be the most significant driver for change in the maritime sector since coal and steam gave way to fuel oil. Emissions from fossil fuels come at a price and professional mariners know the legislation relating to marine pollution (MARPOL) plus the serious financial implications of getting it wrong.
Download PDF: Viable Hybrid Power Systems for Workboats >
Hybrid Marine Power & Propulsion Conference - October 2015 >
Fuel and Power for Shipping is Changing
The maritime sector tends to avoid changes until it has to, but the ocean going shipping community could not ignore the emissions regulations that came into force on 1st January 2015.
This may appear a mundane issue but consider the implications as certain types of vessels are banned from entering ports around the world, simply because of their diesel exhaust emissions. This will increase the cost of world trade as a high percentage of all goods are transported by sea.
The diesel in ships tanks is now getting so light and highly treated that navies are able to run their RHIBs and boats on diesel from the mother vessel. While conventional oil based fuels remain the main fuel option for most in service vessels, Liquid Natural Gas (LNG) is now a proven and available fuel solution for ship propulsion. The commercial opportunities of LNG are now gaining interest for new builds and conversion projects. If LNG does not fit their needs ship operators will consider installing hybrid power systems alongside of their diesel engines. Meanwhile innovative energy solutions may have been ignored in the sub IMO (sub 24 metre / sub 80 feet) workboat sector if they are only viewed negatively as part of a complicated and costly compliance process.
Workboats Can Learn From Automotive
The race to provide electric power for the highly competitive automotive industry has given battery manufacturers the commercial reason to rapidly improve their technologies. Tesla electric cars can now cover over 200 miles on a single charge. However sales of electric cars are held back by the lack of infrastructure for charging and as many European governments have no spare money for incentives or subsidies the roll out will remain slow.
This is good news for hybrid car producers. Particularly when cars can simply be charged at home overnight and when parked at work during the day. If the journey is longer than the battery range then the gasoline or diesel engine takes over. This will be another factor that accelerates the demand for hybrid diesel / electric vehicles, that switch to battery powered electric drive in town. In the workboat sector there is already a potential charging infrastructure with dockside power and operating ‘in town’ has similarities to ‘in port’.
Diesel / Electric Ships are not Hybrids
Diesel / electric systems have been used in large ships and submarines for many years but these are not hybrid systems. The diesel / electric vessel uses its engines to connect directly to an electrical generator. The power in the system is then transferred electrically to the propeller shaft via a motor controller and electric motor. The system may have multiple generators and multiple motors. By strict definition this is not a hybrid as there is no storage of electric energy.
Serial and Parallel Hybrid Power Systems
There are two main types of hybrid system. Firstly a serial hybrid, where the engine in the system only powers a generator and is not mechanically connected to the propeller shaft. Secondly a parallel hybrid, where the engine is mechanically connected along with an electric 'machine' that can operate as both a propulsion motor and a generator.
The reduced electric propulsion, generator and battery demands of a parallel system substantially reduce the cost compared to a serial system. Parallel systems are more likely to win initial market acceptance because of a perceived greater reliability, as the ‘trusted’ diesel engine is still connected to the propeller shaft with the electric propulsion adding a redundant system.
Until recently it has not been possible to transfer such systems successfully to smaller craft. A European Union funded project called HYMAR (High efficiency hybrid drive trains for small and medium sized marine craft) set out to develop an optimised hybrid system. The conclusion at the end of stage one was that the initial focus on ‘serial hybrid’ systems had been misplaced, and that the project's objectives would be better met by ‘parallel hybrid’ systems. As stage two HYMAR developed a parallel hybrid system that has been installed, tested and validated on marine craft. HYMAR has also built a comprehensive energy management module and graphical user interface to control the energy flows of an entire craft. The optimised hybrid system developed during the project offers three major advantages - no detectable emissions, no discernible noise and a substantial reduction in fuel consumption.
Hybrid Power in the Workboat Sector
We are entering a period of rapid change and commercial opportunity in the hybrid marine market. Owners and operators can now consider various hybrid systems with marine applications. DNV-GL USA recently stated that, ‘energy storage is an exciting new technology, but the offshore E&P sector of the oil and gas industry has yet to truly take advantage of it. Tugboats, workboats and OSVs are particularly suitable for hybridization.’ Benefits include improvements in energy reliability, increased fuel efficiency, lifecycle cost reductions and reduced emissions.
Marine Electric Motors Need Smart Battery Power
Battery powered electric motors have been available on small craft for many years. But until recently electric outboard motors had been mainly under 10hp for small fishing boats, tenders and kayaks. The main obstacles to overcome before scaling up had been battery technology and the high initial cost of procurement. Deep Blue is an electric drive system that has been industrially developed and manufactured by the German company Torqeedo, using high-tech components. The system is available as 40hp and 80hp inboard or outboard versions.
Next Generation Cells & Batteries
The next generation of cells and batteries are key technology developments that are making marine hybrid systems potentially viable. Battery chemistry such as Lithium-ion offer impressive power solutions and the business case is starting to fit for commercial operators. Since there is no single system that fits every application it is important to work with manufacturers that have flexibility in cell manufacturing and offer scalable solutions. New factories with fully automated processes ensure consistently high quality cells and quality control of the entire battery management system.
Michigan based XALT Energy offer several variants of High Energy, High Power, and Ultra Hi-Power cells. Robert Young, Technical Lead for Marine Applications at XALT Energy, said, ‘our team of engineers have worked to the highest standards developing electric and hybrid energy solutions for the US and global automotive sector. XALT Energy not only has the necessary knowledge, but also the experience of taking high voltage battery projects from concept through production into the finished system.’
Integrating High Voltage Battery Systems on Boats
Battery banks require space and as they not usually replacing another component this can be an issue for smaller craft. Naval architects require additional weight to be low and central for most designs of small craft. Once the onboard space and footprint are allocated battery designers and engineers need to consider issues specific to marine applications. These include shock and vibration when a boat is underway plus the challenges of installing high voltage systems in enclosed spaces. Although modern batteries are expected to have a long life, they need to be carefully positioned to enable access for inspection. Integration needs to consider onboard safety plans and risk management regarding crews, passengers and critical systems.
Cost / Benefit implications will start with the initial purchase of the system then work out payback period based on the life cycle of the vessel and life cycle of the hybrid power system. Once a system is defined projections and audits can be based on engine management data linked to work cycles. Hybrid systems are infinitely scalable which enables owners to specify what they are trying to achieve over a period of time or an entire fleet.
Electric & Hybrid Opportunities for Retrofit and New Builds
When studying work cycles of vessels it is relatively straightforward to make a decision for new builds on whether to go for all electric or a diesel / electric hybrid system. For example a ferry operating over a short route with a long stopover each end could offer the perfect work cycle for ‘electric only’ with a land based charging system. Other issues, such as the cost of downtime and structural alterations affect viability calculations for retrofit of in-service craft.
Hybrid Systems and ‘The Hour Of Power’
Certain maritime sectors are potentially well suited to ‘hybrid’ diesel / electric systems. These include wind farm service vessels (WFSV) and pilot boats that have relatively consistent duty cycles, often running seven days a week to drop off or collect technicians and pilots.
Indentifying the viability of hybrid diesel / electric power for offshore wind farm support vessels is an interesting project that links green energy onboard with renewable energy from the environment. Hooking up to offshore wind farm turbines may even provide charging options.
The first objective is to focus on the sub IMO (sub 80 feet) workboat, pilot boat and patrol craft sectors to investigate the engineering and systems integration required to bring together viable and sustainable solutions. With vessel life cycles of over 20 years, naval architects and builders of new craft will offer designs that have space and access routes to enable retrofit of hybrid installations. Speed limits in harbours and channel approaches at beginning and end of daily transits may mean that ‘The Hour Of Power’ is all that is required for the electric part of the cycle.
Hybrid Power & Propulsion Systems for Workboats
BAE Systems HybriDrive is a provider of hybrid propulsion systems with technical experience in hybrid technology for land based applications. BAE Systems aims to partner with manufacturers of marine diesel engines to provide complete propulsion and auxiliary power systems to increase the operating efficiency and performance of a vessel, while reducing fuel costs and emissions.
ZF Marine offers a range of hybrid-ready transmissions and propulsion for larger fast craft applications. The design is based on a unique Power Take In (PTI) configuration, allowing highest flexibility for customizing installations. These transmissions can be integrated into hybrid propulsion systems for all types of fast craft, from coast guard vessels to fast offshore supply vessels.
Siemens have extensive experience of hybrid and electric technology for various modes of transport. Siemens offer both series and parallel hybrid systems for the commercial marine market. Siemens supplies all components related to the electrical propulsion system including the drives, generators, inverters, filters, and control system, plus step up gearboxes to attach the generator to diesel motors.
Hybrid Power Technicians in the Shipyard
There are clear opportunities related to problem and solution however the integration of products will be crucial. There will be a new career in shipyards for ‘Hybrid System Integrators’. These will be individuals and teams that have a holistic approach to engineering and many will need to be qualified high voltage technicians. When integrating hybrid systems a shipyard will need to identify which competencies are required. To warranty the system it will need to define who signs off the installation and the components on handover. Manufacturer’s liability is a commercial reality that can be hidden behind factory recalls on land, but at sea a single point of failure will reflect on all OEMs in the hybrid power ‘system’.
Implications of Legislation and Standards
Various legislation and standards have implications for end-user organisations, boat builders and equipment manufacturers. As cells, batteries, power generation and storage evolve it is important to address misconceptions and myths to enable progress. For example Lithium Ion has been part of our lives in non-marine sectors for many years as the battery power behind electric cars, city busses, smart phones, tablets, laptops and cameras.
Besides how to present performance metrics it will be essential to identify whether current standards from land based applications are valid. An environment with electricity, water and damp enclosed spaces requires specific testing and sea trial standards. A new ISO standard for high voltage DC propulsion systems and comprehensive energy management in maritime environments will be relevant.
Power and propulsion systems that are designed and built for professional or commercial operations need to run hard, often for long hours in adverse sea conditions. Users must be able to rely on these systems at all times. In certain situations failure is not an option – the engineering must not break. Professional boat operators around the world have learned that power and performance are relevant, but reliability and durability are important factors for all types of engine and propulsion.
Effective Integration and Global Partnerships
The Hybrid community will need to engage with diesel engine manufacturers. New high tech companies entering the market will want to utilise the existing relationships that diesel engine OEMs have with end-users, boat builders and standards agencies. The importance of an international service, spares and support network will add confidence to procurement and life cycle maintenance decisions.
If the marine industry wants to move forward quickly it will have to build teaming agreements and partnerships that bring together technologies. Hybrid marine will not tolerate inferior parts. All components will need to be built to the highest industry standards and designed to integrate globally across multiple platforms.
Download PDF: Viable Hybrid Power Systems for Workboats >
Hybrid Marine Power & Propulsion Conference - September 2015
Shock Mitigation have brought together a group of experts armed with the latest knowledge that will assist the sub IMO (sub 24 metre / sub 80 feet) professional sector to understand the possibilities of utilising hybrid systems.
Shock Mitigation Workshops - Connecting the Disconnected
The Conference sessiona are designed to engage with various stakeholders including end-user organisations, boat owners, boat operators, boat builders, engine manufacturers, mechanical & electrical engineers, naval architects, maritime legislators and government bodies.
The objective is to create affiliations that share engine data, battery capabilities and work cycles for vessels. The aim is to identify the potential for hybrid systems for specific sectors, starting with diesel / electric for wind farm support vessels, pilot boats, patrol craft, workboats, survey vessels and unmanned craft.
Building Networks & Accelerated Knowledge Transfer
For OEM engine manufacturers, component suppliers and installers the take away knowledge from these sessions will be relevant to various departments including strategic product development, engineering and business development.
The capabilities and expertise are already in separate companies. Due to the range of technologies required it is unlikely that any one manufacturer will provide a complete system.
For end user organisations, including owners and operators, this knowledge will help to shape decisions that lead to procurement of next generation vessels and improvements to in service systems.
Hybrid Marine Power & Propulsion Conference - October 2015 >
John Haynes is an Associate Fellow of the Nautical Institute, Yachtmaster Ocean and Advanced Powerboat Instructor. Subject matter expertise includes high speed craft consultancy, product development and specialist training.
He is Operations Director of Shock Mitigation www.shockmitigation.com and founder of the RIB & High Speed Craft Directory that brings together specialist boats and equipment for the professional sector www.ribandhsc.com
All images are copyright NEXT GEN Marine Ltd 2025 unless otherwise stated.
This does not exclude the owner's assertion of copyright over the material.